13 Mar Најдобрите пет убијци на продуктивноста во индустријата за ПХБ
Некои решенија
Патот до максимизирање на продуктивноста на фабричките подови лежи во пристапот од горе надолу кој се однесува на деталните оперативни точки во претходните делови. Треба да се преземат чекори во следните области: Подготовка на податоци Симулација на производниот процес Подготовка на производствен процес Системи за извршување на производство Потребни се технички решенија за сите овие предизвици. И, најважно, мора да се воспостават системи за известување за инженерите, линиските оператори и производствените менаџери кои ги идентификуваат конкретните активности што треба да се преземат за да се подобрат перформансите. Покрај тоа, информациите мора да бидат доволно навремени за да овозможат подобрувања пред да се изгуби можноста и да се појават нови проблеми на друго место. Подготовка на податоци Вниманието на подготовката на податоците и за внесувањето на моделот на компонентите и за внесувањето податоци за дизајнот е задолжителен прв чекор: Моделирање на компоненти - Производителите треба да воспостават точно физичко моделирање на сите делови што планираат да ги користат на линијата, вклучително и контактите со пинови за лемење спојници, интегрирани со CAD податоците. Ова треба да содржи: Конзистентно, CAD-библиотека неутрално, моделирање на деловите за да се овозможи стандардизирана функција на DFM и подготовка на процесот низводно. Нормализирано поместување на компонентите, ротации и изјави за поларитет до стандард. Светската електронска индустрија има продажба од 750 милијарди американски долари, од кои две третини отпаѓаат на склопување на ПХБ. Производството на ПХБ се карактеризира со опсесивен нагон за зголемена продуктивност во контекст на три значајни индустриски двигатели: Пократок животен циклус на производите - Притисокот е да се развијат подобри производи и да се донесат на пазарот пред конкуренцијата, со пониска цена, а истовремено да се развива производ од следната генерација. Пред само пет години, животниот циклус на производот беше измерен во години; сега тие се мерат во месеци, со што се врши притисок врз дизајнерите и производителите да го забрзаат процесот на преминување од фаза на прототип до производство со голем обем. Покомплексност – Производителите произведуваат посложени дизајни со поголема густина со зголемена минијатуризација и пософистицирани табли. Типична сметка за материјали (BOM) за склоп на ПХБ сега може да има вкупно илјадници делови, составени од стотици уникатни ставки. „Купените“ ставки – кондензатори, отпорници, диоди и така натаму – ќе имаат по еден или повеќе „алтернативни делови“ за да се овозможи минимална цена на BOM и максимална достапност на делови. Покомплексните сметки за материјали (BOM) даваат предност на зголемениот квалитет на компонентите и подобрата следливост. Аутсорсингот расте брзо - Пократкиот животен циклус на производите и зголемената сложеност ги принудија OEM да го прифатат аутсорсингот, сега најбрзо растечкиот сегмент од индустријата за ПХБ. Компаниите за производство на електроника (EMS) сочинуваа 21% од пазарот во 2004 година, но нивниот удел ќе достигне околу 30% до 2008 година. Пазарот севкупно ќе порасне само 16% за тоа време. Давателите на EMS нудат пониски цени, забрзана брзина до пазарот и подобри перформанси за исполнување на нарачките, бидејќи тие ја користат огромната збирна куповна моќ добиена од опслужување на стотици различни клиенти и преку консолидирање на нивните производствени средства и управување со нив за да постигнат минимални единечни трошоци. Давателите на EMS се фокусираат на нивната основна компетентност за производство и набавка на компоненти; ОЕМ можат слободно да се фокусираат на дизајнот и маркетингот на нови производи. Овие индустриски трендови се добро разбрани и придонесоа склопувањето на ПХБ да стане една од најконкурентните индустрии во светот. Со притисок да се намалат трошоците, а истовремено да се подобрат приносите и брзината на пазарот, се бара промени во работењето на фабричките подови кои можат да ја подобрат конкурентноста. Вообичаено, 60-70% од инвестираниот капитал на основни средства во операциите на склопување на ПХБ е затворен во машините во склопувачките линии. Склопувањето на SMT е особено интензивно на капитал, на пример, со единечни линии кои чинат повеќе од 1 милион американски долари и цената се зголемува. Менаџерите на производствени погони се прашуваат како можат да обезбедат нивниот вложен капитал да обезбеди максимална продуктивност и конкурентност. Одговорот лежи не само на ниво на поединечни машини, туку и на ниво на целосна линија или фабрички под. Склопувачите на ПХБ користат многу мерења на производните перформанси од спецификите на нуспроизводот на производот за време на циклус, брзина на отчукување на линијата и принос на прво поминување, до репери на повисоко ниво како што се „трошок за конверзија на BOM“ и поврат на користениот капитал. Без оглед на тоа што се користат клучните показатели за изведба (KPI), целта е да се генерира максимален резултат на прифатлив квалитетен производ од достапните линии за склопување, материјали, тела и човечки ресурси што се достапни.
- Хаос на делови
- Неефикасно поставена линија
- Побавни од оптималните стапки на отчукување
- Машински максимални перформанси
- Комбинацијата ПХБ/процес е под-оптимална
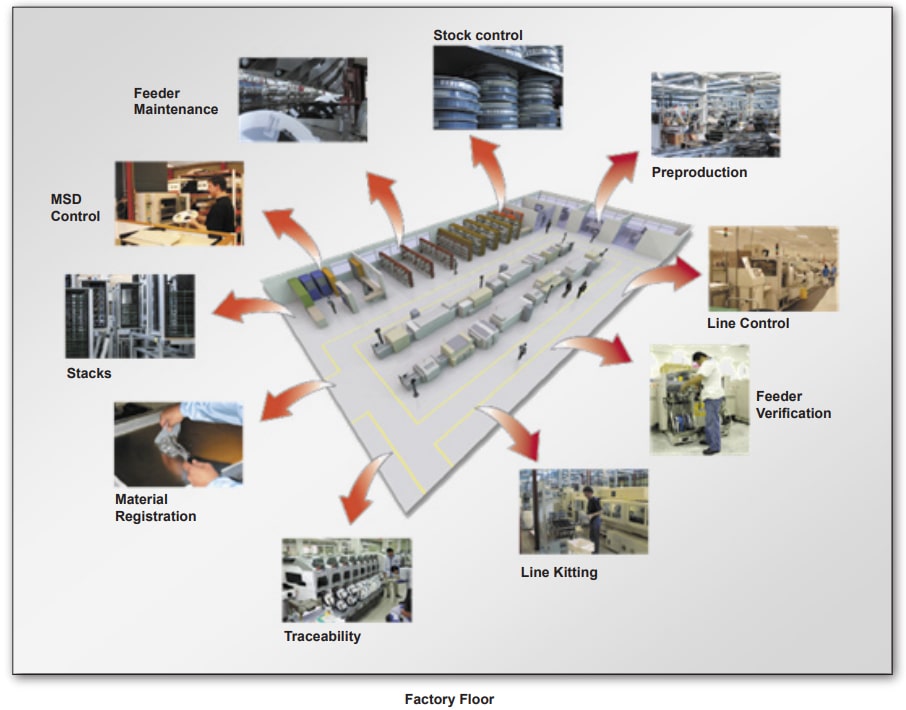
- Хаос на делови Првото прашање што влијае на продуктивноста е тоа што материјалите не се на вистинското место во вистинско време, подготвени за употреба на монтажните ленти. Многумина веруваат дека е доволно да се има целосна покриеност во ERP или главниот систем за контрола на акции на сите BOM што треба да се склопат. Но, критичниот фактор е да се имаат достапни точни количини на делови и материјали и да се инсталираат на машините во точното време кога е потребно. Проверката на достапноста на броевите на деловите на компонентите масовно не го спречува неуспехот во производството поради недостапност на делови на фабричкиот под затоа што:
i. Делови кои се веќе посветени на други поставки - компонентите за склопување на ПХБ обично се ракуваат на големо - или во ролни што држат илјадници делови или во купишта фиоки со стотици. Ако истите делови се потребни истовремено за две производствени нарачки, ниту една линија не може да се постави правилно. Умножувањето на влијанието на овој проблем на стотиците макари или фиоки за компоненти присутни на типичен фабрички под на ПХБ, го зголемува ризикот од неможност да се испорачаат вистинските количини на делови до линиите за секоја производна нарачка, и покрај фактот што збирно , потребните вкупни количини на делови за нарачките за производство се совпаѓаат со вкупните количини на делови во главниот систем за контрола на залихите.
II. Достапните делови не можат да се најдат - Често, во големите фабрики, ERP системите не ги следат многу прецизно материјалите откако ќе бидат пуштени на производниот под. Клучните податоци – во врска со линијата на која се доделени деловите, дали поставките за кои се обврзани сè уште се во производство и точното количество делови што биле врзани во тие поставки – често недостасуваат. Иако достапните податоци покажуваат дека деловите се достапни за почеток на производството, тие често не можат да се лоцираат. Непотребните доцнења се резултат на почетокот на производството, додека „експедиторите“ френетично бараат материјал што недостасува. Подеднакво, и поради истиот недостаток на видливост за тоа кои делови се наоѓаат, често делови може непотребно да се испорачаат на линија, за да се поддржи поставувањето, кога всушност доволно залихи од тие делови е веќе натоварено на линијата, остаток од претходна нарачка за производство. Овие неточности во следењето резултираат со непотребни зголемувања на трошоците за залихи на фабричките подови. поради промашени избори или дефект на млазницата пред поставувањето. Во голема мера, ова ги принудува производителите на ПХБ на преценување
III. Делови во карантин - Друг фактор што влијае на достапноста на деловите во машината за собирање и ставање е чувствителноста на некои категории компоненти на изложеност на нормални атмосферски услови на фабричкото под. Понекогаш компонентите се под влијание на атмосферската влажност по отпакувањето од затворените садови и, по само неколку часа, тие мора да се печат во рерна за да се отстрани влагата од телата на компонентите. Дисконтинуитетите предизвикани од циклусите на печење во рерната значат дека одредени делови поминуваат низ циклуси на „достапни“ и „недостапни“ за склопување, иако тие се „на залиха“ цело време.
iv. Неточна контрола на залихите – Достапноста на залихите на делови во системот ERP често е неточна како резултат на неевидентирано трошење. Кога компонентите се враќаат во магацинот по употребата на фабричкиот под, проблематично е да се собере точна слика за тоа колку делови остануваат на макарата. Дали менаџерите на производство треба едноставно да ја земат почетната количина и да го одбијат бројот на пласмани дефинирани на BOM? Веројатно не, бидејќи ги игнорира деловите изгубени од нивоата на залихите на машината, што доведува до неочекувани залихи на фабричкото под во следните производствени нарачки. Скапите (и непланирани) исклучувања на производството како овие создаваат потреба да се исчистат материјалите од линиите за последователни нарачки и итни набавки на делови за да се поправат недостатоците. Неточната контрола на залихи, исто така, принудува на одзема време и скапа практика на ревизии на залихи на целата локација, кога производството е суштински ставено на чекање додека записите во системот ERP рачно се синхронизираат со реалноста на производниот под.
v. нивоа на залихи, што доведува до неочекувани залихи на фабрички под во следните производствени нарачки. Скапите (и непланирани) исклучувања на производството како овие создаваат потреба да се исчистат материјалите од линиите за последователни нарачки и итни набавки на делови за да се поправат недостатоците. Неточната контрола на залихи, исто така, принудува на одзема време и скапа практика на ревизии на залихи на целата локација, кога производството е суштински ставено на чекање додека записите во системот ERP рачно се синхронизираат со реалноста на производниот под.
- Неефикасно поставување на линија Ефикасната линија за склопување SMT зависи од способноста да се координираат стотици променливи за поставување истовремено. Ако некој аспект од поставената линија е неточен, резултатот е резултатот со слаб квалитет. Постојат неколку вообичаени причини за бавно поставување и дебагирање на линијата:
i. Инструкциите за поставување не се совпаѓаат со машинските програми - Во многу случаи, инженерските податоци што пристигнуваат на линиите доаѓаат од повеќекратни, исклучени текови на податоци. Списокот за комплетирање за секоја машина е воден од BOM во системот ERP, но сепак не ги зема предвид одлуките за разделување и балансирање на BOM што ги преземаат машинските програмери. CAM системите што се користат за генерирање машински програми често работат од различна база на податоци од CAM системот што се користи за генерирање на фабрички патник на подот. И CAM системите што се користат за програмирање на машините AOI се различни од системите што се користат за програмирање на машините за собирање и поставување. Фрагментацијата на тековите на податоци може да биде обемна; секоја точка на исклучување помеѓу инженерските бази на податоци нуди уште една можност за генерирање несинхронизирани податоци или инструкции за различни делови од склопувачките линии. Сите грешки во поставувањето треба или да се отстранат на изворот, според дизајнот или да се откријат во фазата „прв почеток“ и да се отстранат со уредување инструкции за поставување додека линијата е исклучена и непродуктивна
II. Податоците за делови на машините недостасуваат или се неточни – на секоја SMT машина за собирање и поставување, AOI машина и тестер во коло им е потребна библиотека со податоци за да се опишат клучните карактеристики на секоја компонента што треба да се состави, проверува или тестира. Само кога библиотеката на компонентите на машината е исполнета со податоци што ги опишуваат компонентите за нарачката за производство, машината може да ја заврши својата работа. Секој нов дел вчитан на фабричкиот под значи дека библиотечните податоци за тој дел мора да се внесат во машините и да се проверат. Откако ќе се создадат, податоците мора исто така да се управуваат правилно бидејќи сите направени промени потенцијално може да резултираат со непотребно време на прекин ако не ги изврши квалификуван оператор. Без контролирано и централизирано решение за управување со податоците за компонентите на ниво на машина, податоците мора макотрпно да се внесуваат во повеќе машини, предизвикувајќи непотребно прекинување и висок ризик од неусогласеност на податоците помеѓу повеќе машини.
III. Целосното офлајн поставување не е постигнато – Многу производители не се способни за офлајн вчитување на компоненти и проверка на поставување. Ова ја принудува линијата да се спушти и да се постави за да се преземе пред да започне производството, што доведува до непотребно време на застој. Без сомнение, вкупниот трошок за залиха на фидер може да се минимизира со поставување на on-line, но се плаќа висока цена во однос на изгубената линија и искористувањето на машината.
iv. Поставувањето е неправилно во фазата на прв пат - Ако целокупното поставување на линијата не е потврдено паралелно со проверката на залихите на самиот почеток, грешките мора да се откријат во моментот на производство на првото излегување. Ова е најскапиот начин за наоѓање и елиминирање на грешка при поставувањето, бидејќи изминатото време помеѓу создавањето на грешката и откривањето е максимизирано. Помножете ги можностите за грешка/откривање/поправање според бројот на фидери, машини, програми и можноста за ескалирање на времето за отстранување грешки на поставувањето станува јасна, во споредба со потврдувањето на секој аспект од поставувањето додека се изведува. Откако ќе заврши првата фаза на исклучување и линијата е целосно во производство, исто така е од витално значење да се избегнат грешките кога се ставаат нови делови на машината за да се надополни исцрпениот фидер. Во најлош случај, неправилно поставените делови ќе бидат откриени по склопувањето на целата серија, во фазата на проверка или тест. Ваквите поправки имаат максимална цена и влијание врз целокупната продуктивност на фабриката.
v. Неискористување на постојните поставки на машината – Најдобар начин да се минимизира времето на поставување е да се елиминира потребата да се отстранат линиите и повторно да се постават помеѓу производствените нарачки. Поради сложеноста на управувањето со огромната разновидност на компоненти, фидери, позиции на фидери, количини на компоненти и факторите кои влијаат на оптимизираното поставување за минимално време на циклус, повеќето производители ги отстрануваат сите фидери и компоненти од линиите помеѓу производствените нарачки. Ова ја одржува контролата, но драматично ја намалува продуктивноста. Со однапред анализирање на нарачките за производство и идентификување на групи производи кои можат да го делат истото поставување (или поголемиот дел од поставувањето) на склопувачка линија без да се жртвува брзината на отчукување до неприфатлив степен, може да се постигнат огромни заштеди во времето на застој. Користењето техники за групирање производи обезбедува значителни подобрувања во продуктивноста во операциите со висока мешавина/мал до среден волумен, каде што менувањата се еден од главните придонесувачи за застојот на линијата.
VI. Неуспех да се предвидат барањата за надополнување на делови - Во производствени средини со голем волумен, ниска мешавина, недостаток на однапред за точен пристап заснован на симулација за програмирање на линијата како целина. ii. Машинското програмирање не се заснова на целосна кинематска симулација – Ако симулацијата и програмирањето (балансирањето) на ниво на линија се одделат од машинското програмирање, ќе има конфликт меѓу двете; балансирањето зависи од точните информации за поединечните времиња на циклуси, а програмирањето на машината може да генерира различно време на машински циклус од она што го претпоставува функцијата за балансирање на линии. Клучот е многу прецизна симулација на конфигурацијата на секоја машина (внесувачи, млазници, ...) и нејзината кинематика на движење. Без точност во симулацијата на времето на машинскиот циклус, не само што ќе страдаат индивидуалните перформанси на машината, туку и целокупната линија нема да биде избалансирана за оптимален севкупен излез. видливоста на потребата за надополнување на делови на линијата е единствената најважна причина за застојот. Најлошиот случај се случува кога сите компоненти во фидерот се исцрпени, но тоа е изненадување за линискиот оператор (кој треба да надгледува стотици фидери истовремено). Ова ја принудува линијата надолу додека фидерот е отстранет, се наполнува нова ролна (претпоставувајќи дека е при рака) и фидерот повторно се вчитува на машината.
- Побавни од оптималните стапки на отчукување Откако линиите ќе се постават, производството се населува во неговиот повторлив ритам, при што собраните ПХБ излегуваат од линијата со фиксна фреквенција одредена од балансот на линијата, способностите на машината и нивото на оптимизација вградено во производот- самите специфични машински програми. Во овој момент, продуктивноста е засегната на скап, но невидлив начин, доколку линиите не се програмирани да работат со максимална можна брзина на отчукување. Ова може да се случи поради неколку причини: i. Симулацијата, разделувањето/балансирањето на BOM и програмирањето на машината не се изведуваат на ниво на целосна линија - Одделни машини може да се програмираат на оптимално ниво, но ако не се примени пристап со целосна линија кон програмската задача, врз основа на целосна кинематска симулација од сите машини што ја сочинуваат линијата, севкупните перформанси страдаат, првенствено предизвикани од нерамнотежа на машинскиот обем на работа. Времето на циклусот, или брзината на отчукување, на линијата се одредува од најбавната машина во линијата, нагласувајќи ја потребата за точен пристап базиран на симулација за програмирање на линијата како целина.
II. Машинското програмирање не се заснова на целосна кинематска симулација – Ако симулацијата и програмирањето (балансирањето) на ниво на линија се одделат од машинското програмирање, ќе има конфликт меѓу двете; балансирањето зависи од точните информации за поединечните времиња на циклуси, а програмирањето на машината може да генерира различно време на машински циклус од она што го претпоставува функцијата за балансирање на линии. Клучот е многу прецизна симулација на конфигурацијата на секоја машина (внесувачи, млазници, ...) и нејзината кинематика на движење. Без точност во симулацијата на времето на машинскиот циклус, не само што ќе страдаат индивидуалните перформанси на машината, туку и целокупната линија нема да биде избалансирана за оптимален севкупен излез.
III. Податоците за деловите на ниво на машината не се програмирани за оптимални перформанси на ракување - Податоците за деловите што ги користи секоја машина дефинираат како да се ракува со компонентите: со која брзина, со која млазница, колку долго треба да бидат различните времиња на задржување, кои поместувања треба да се применат на точката за подигнување и така натаму. Завршувањето на првото исклучување е доволно за да се потврди дали производот е правилно склопен, но тоа не изложува никакви ефекти со мала брзина на склопување поради неоптималните упатства за ракување вградени во библиотеката со податоци за делови на машината. Операторот понекогаш ќе избере да ја намали брзината на поставување на компонентата за да обезбеди склопување, често прикривајќи ги проблемите со одржувањето што треба да се решат додека значително ја намалува целокупната продуктивност на линијата. Како и со оптимизацијата на самите машински програми, без пристап до детални податоци за перформансите е практично невозможно луѓето да ги идентификуваат овие ефекти; а без детекција не можат да се коригираат.
- Максимални максимални перформанси на машината Со инвестиции во линии до милиони долари, јасно е дека машините треба да се одржуваат да работат со максимална продуктивност за максимално време. Сепак, постојат многу аспекти на состојбата на машината кои имаат подмолен ефект врз намалувањето на севкупните перформанси.
- Вакуумски притисок во млазницата – Ако ова е надвор од спецификациите, предизвикува паѓање на компонентите при транзит помеѓу точката за подигање и нивната положба на ПХБ.
- Префрлување вакум со леплива млазница – Ако прекинувачот за вакуум е леплив, тоа доведува до прескокнување на прскалките. За да се одберат компонентите од фидерот без грешка, потребно е позитивно и брзо префрлување на доводот на вакуум до прскалките. Истото важи и за поставувањето; бавното или непрецизното префрлување на вакуумот предизвикува непрецизно подигање или поставување.
- Истрошени колибри – Ова води до високи стапки на промашување на чепкање. Компонентните фидери се механички уреди за индексирање кои се трошат со текот на времето. Како што механизмот се истроши при нормална употреба, точноста на прикажување на компонентата за подигање опаѓа, што доведува до неправилно земање, што ги троши компонентите и времето на циклусот. iv. Лоши упатства за одржување - SMT линиите ги поставуваат компонентите со брзина од десетици или стотици илјади делови на час. Оваа брзина на молскавична машина го отежнува набљудувањето на опаѓачките перформанси. Избирањата за промашување се случуваат премногу брзо за да се видат, но доцнењето од неколку милисекунди на функцијата што се повторува доведува до детонирани перформанси. Без прецизно и навремено известување за тоа каде се намалуваат перформансите, линиските оператори и персоналот за одржување имаат мали шанси да преземат вистинска акција за да ги подигнат перформансите.
- Лоши упатства за одржување - SMT линиите ги поставуваат компонентите со брзина од десетици или стотици илјади делови на час. Оваа брзина на молскавична машина го отежнува набљудувањето на опаѓачките перформанси. Избирањата за промашување се случуваат премногу брзо за да се видат, но доцнењето од неколку милисекунди на функцијата што се повторува доведува до детонирани перформанси. Без прецизно и навремено известување за тоа каде се намалуваат перформансите, линиските оператори и персоналот за одржување имаат мали шанси да преземат вистинска акција за да ги подигнат перформансите.
- брзината на молња машина го отежнува набљудувањето на опаѓачките перформанси. Избирањата за промашување се случуваат премногу брзо за да се видат, но доцнењето од неколку милисекунди на функцијата што се повторува доведува до детонирани перформанси. Без прецизно и навремено известување за тоа каде се намалуваат перформансите, линиските оператори и персоналот за одржување имаат мали шанси да преземат вистинска акција за да ги подигнат перформансите.
- Комбинацијата на ПХБ/процес е потоптимална ПХБ-ите можат да бидат дизајнирани да бидат пријателски настроени кон процесот на склопување или непријателски настроени кон процесот. Повеќето ПХБ на крајот може да се склопат, но повисоките трошоци отколку што е потребно поради неоптималниот дизајн, нивоата на преработка и ефикасноста на линијата варираат како резултат на дизајнерските карактеристики како што се:
i. ПХБ-ата не е погодна за машината или линијата - фидуалните податоци се скриени, компонентите се во конфликт со транспортерите, дизајнот на панелот за склопување не е лесен за оптимизација. Дизајнерските ограничувања, како што се дистрибуцијата на компонентите на таблата, или разновидноста на BOM, се такви што еден тип на машина не може да постигне ниска цена за поставување и тоа не станува видливо додека производот не се стартува на линијата.
II. Дизајнот на матрицата за лемење води до неоптимални споеви за лемење - Ова резултира со голема преработка. Примарната цел на склопувањето е да се создадат сигурни споеви за лемење. Освен добрата контрола на процесот на лемење, комбинацијата на иглата на компонентата, шаблонот за лемење и отворот на матрицата за лемење мора да се оптимизира за да му се даде на процесот најдобри шанси да постигне споеви кои се во рамките на прифатливите толеранции (обично мерени во десетици лоши споеви, на милион произведен милион).
iii. Распоредот на дизајнот на ПХБ поттикнува наведнување и извртување - Панелите на ПХБ поставени на линијата за склопување треба да бидат совршено рамни, за да се избегнат „закачување“ на транспортерот и грешки при обработката во машините. Со дизајнирање на ПХБ со рамномерна распределба на бакар во сите оски, ќе се минимизира тенденцијата на ПХБ да се наведнува и искривува за време на обработката.
iv. Шемите на подлоги/петека го поттикнуваат поставувањето на надгробните камења за време на повторното обложување - Со трендот кон помали пасивни компоненти на чипот, како што се пакетите 0201 што сега се ракуваат во волумен, дизајнот на шаблоните на подлогата и патеката за да се овозможат еднакви ефекти на потопување топлина на двете страни на компонентата е од зголемено значење. Како што компонентите стануваат полесни, ефектот на ефектите на површинскиот напон за време на повторното течење станува се поважен; ако едната страна повторно тече пред другата, површинскиот напон може да предизвика подигање на сувата страна на спојницата, предизвикувајќи ефект на „надгробна плоча“.
Некои решенија
Патот до максимизирање на продуктивноста на фабричките подови лежи во пристапот од горе надолу кој се однесува на деталните оперативни точки во претходните делови. Треба да се преземат чекори во следните области: Подготовка на податоци Симулација на производниот процес Подготовка на производствен процес Системи за извршување на производство Потребни се технички решенија за сите овие предизвици. И, најважно, мора да се воспостават системи за известување за инженерите, линиските оператори и производствените менаџери кои ги идентификуваат конкретните активности што треба да се преземат за да се подобрат перформансите. Покрај тоа, информациите мора да бидат доволно навремени за да овозможат подобрувања пред да се изгуби можноста и да се појават нови проблеми на друго место. Подготовка на податоци Вниманието на подготовката на податоците и за внесувањето на моделот на компонентите и за внесувањето податоци за дизајнот е задолжителен прв чекор: Моделирање на компоненти - Производителите треба да воспостават точно физичко моделирање на сите делови што планираат да ги користат на линијата, вклучително и контактите со пинови за лемење спојници, интегрирани со CAD податоците. Ова треба да содржи: Конзистентно, CAD-библиотека неутрално, моделирање на деловите за да се овозможи стандардизирана функција на DFM и подготовка на процесот низводно. Нормализирани искази за поместување, ротации и поларитет на компонентата до стандард.
Нема коментари